Managing your Supply Chain Must Include the Monitoring of the Effective Delivery of Energy
-
02 November 2016
-
EA Technology
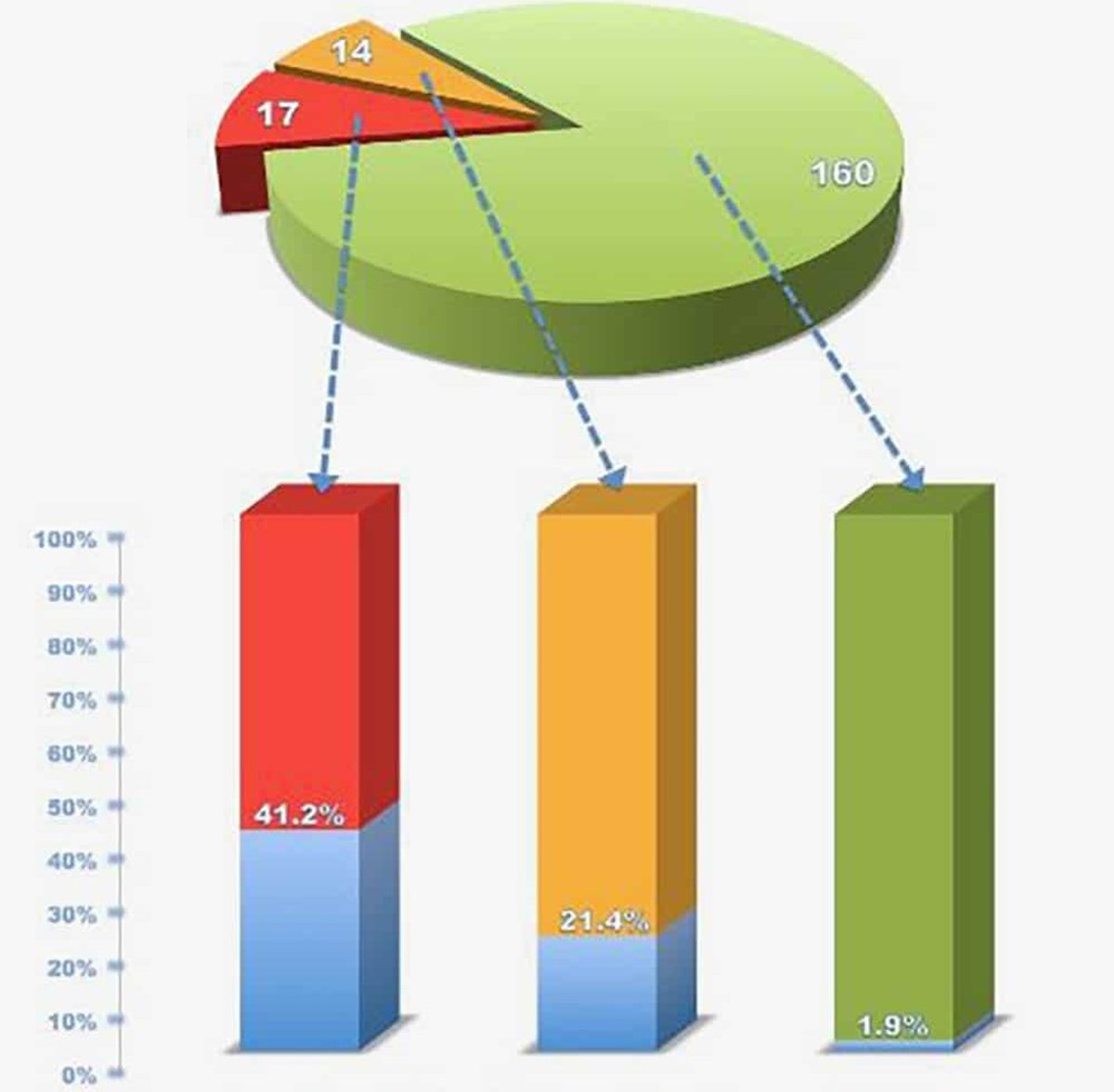
To most manufacturers the management of the supply chain is the ‘just in time’ stock control system of the components required to produce their end product. Effective energy management, whether electricity or gas, is often assessed by the facilities management department on a simple cost to supply basis.
Therefore isn’t it time for you to reassess your energy supply by viewing it as an essential component, whose security of supply is as important as the key elements of your production schedule? After all your contracts with suppliers are likely to include service level agreements covering delivery, stock levels and potentially penalties for the lack of supply. Electricity is the ultimate just in time component; you hold no stock, its delivered to site as need arises and if it fails so does your entire production effort.
It’s down to risk management, it’s down to criticality, and it’s down to the fact that without the high voltage (HV) power grid your factory grinds to a halt.
There are two key constituents to the HV grid; cables and switchgear. Both sit there, slowly deteriorating over time until they are either replaced or fail. There is though a way of identifying those elements that are in danger of failing. Partial Discharge…
Partial Discharge is an electrical discharge or spark that bridges a small portion of the insulation between two conducting electrodes. This is commonly known as Partial Discharge (PD) activity and can occur at any point in the insulation system where the electric field strength exceeds the breakdown strength of that portion of the insulating material. PD can also occur in voids within solid insulation, across the surface of insulating material or within gas bubbles in liquid insulation.
Realistically you do not need to fully understand what PD is, but you do need to understand the benefits that active PD monitoring of your assets can give you. It can give you early warning of potential network failures as well as providing you with a method of justifying your investments and decreasing negative consequences to your business.
With 50 year’s industry experience and expertise, EA Technology has become leaders in PD monitoring technology. Our products have been deployed for both cables and switchgear with strong, factual evidence to support our technology’s superiority. Two of our recent successes have been turned into case studies, with the highlights below;
Cables
EA Technology’s CableData Collector™ was used to carry out a PD assessment of nearly 200 high voltage cables. The assessment was undertaken with the cables energised and tested in a non-intrusive manner. The cables were categorised Red (high risk of failure) – Amber (potential to fail as PD detected, monitor on a regular basis) – Green (PD not detected) according to the Partial Discharge signatures. Of the 17 cables that were categorised Red, over 40% of them developed a fault inside of 2 years. Of the 14 cables that were categorised Amber, 20% of these cables failed within 2 years. Importantly less than 2% of those categorised green had an issue inside the 2 year period.
A Technology’s UltraTEV Monitor™ was installed in a substation for a long term software test. It was not monitored, as it was simply there for software stability testing. The substation failed unexpectedly (at the right hand edge of the trace below), leaving many thousands of homes and businesses without power. The data collected during the test showed that PD monitoring would have given almost 4 months’ notice of the failure.
The graph below shows the results recorded by the UltraTEV Monitor™ at the DNO’s site:

Convinced yet? The key is to get the technology to do the work for you. Periodic inspections give you a snapshot of the asset health at that discrete moment in time. Continuous, and remote monitoring provides greater piece of mind due to detailed trend analysis giving you early warning of potential failure, decreasing financial outlay and also it releases your inspection teams to more productive tasks.
When you assess the cost-benefit for the financial justification, please account for the cost of lost production, the cost to brand reputation as well as the cost of the replacement equipment. Far better to try to avoid the crisis in the first place!