Transformer Breakdown Voltage Strength, When to Replace the Oil
-
10 March 2021
-
EA Technology
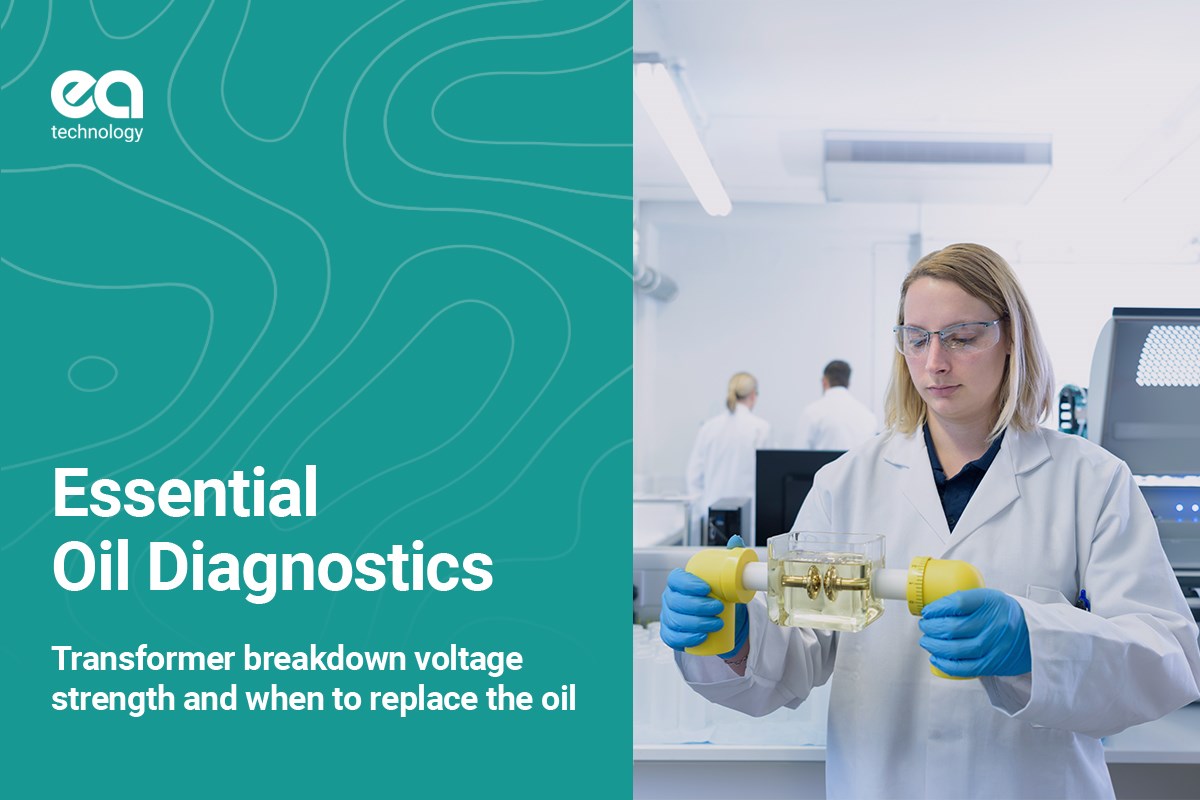
The final part of the basic oil quality assessment trio (along with Moisture & Acidity) is the Breakdown Voltage Strength otherwise known as the BDV.
The BDV is an important factor in understanding the quality of the oil and is affected in many ways. Often there is a direct correlation between a high moisture content and a reduced breakdown voltage so the two should be viewed together to understand what is causing the reduced BDV.
First let’s look at the test itself. The BDV is determined by using a piece of laboratory equipment which is specifically designed for the task, a BDV Tester. The testing is carried out in accordance with IEC 60156: Insulating liquids – Determination of breakdown voltage at power frequency – Test method. In short the test measures the dielectric strength of an oil sample by applying a steadily increasing voltage to the electrodes until breakdown of the oil occurs.
The issues or points of note
The BDV of an oil is inherently variable and is dependent on what aligns between the 2.5mm gap between the electrodes during that specific voltage application. The methodology tries to elevate the variation by carrying out the test six times and gives the average kV which is the one you see on your oil reports.
The size of the test cell…well it’s large! The test cells usually require 350 – 400ml of oil to cover the electrodes and to perform the test on the oil. When the oil samples are typically 500ml sample bottles it doesn’t give much room for manoeuvre. This isn’t so bad for transformers, tap changers and switchgear as you can get a good volume of oil from the units. However, when it comes to cable seal ends etc that’s just not feasible in the real world and therefore creates limitations on what the lab can do. EA Technology have the ability to carry out the BDV on much smaller sample volumes ~35ml , so we are capable of carrying out the tests on most assets with oil in!
Quality of sampling is vital when it comes to BDV. If you pick up particles or contamination from the sample port or environment during the sampling and trap that inside the bottle or oil then that can affect the BDV and it only takes a small amount to reduce it.
What does it tell us?
The BDV assessment gives us information on the contaminants within the oil sample. It doesn’t give a level of contamination just an indication that the oil is contaminated. The BDV is affected by particles which can bridge the gap between the electrodes this particulate can originate from a number of sources such as from the manufacturing process, airborne contaminants, breakdown of insulation and internal components, breakdown of the oil etc.
The moisture content also has an effect on the BDV as previously stated, if the moisture is elevated the breakdown voltage will usually by reduced due to the moisture in the oil bridging the gap between the electrodes which is why they need to be assessed together as part of a group of oil quality tests to understand if the reduced BDV is due to contaminants and particles or in fact due to excessive moisture within the oil.
So when do we replace the oil?
In truth that’s not necessarily the correct course of action as it depends on what the other results are telling us. If the BDV is reduced due to a high moisture content then replacing the oil would not solve the issue…remember where the moisture is held in a transformer, we discussed this earlier in the blog series, a drying process would be required to remove the excess moisture as that’s the cause of the issue.
You would also need to assess the options as there is the option to filter the oil and cycle it back into the asset to remove all the contaminants rather than a straight replacement. Also what is the asset as an oil replacement in a switchgear unit is generally a much easier option than in a transformer asset for example.
There is then also the question of is the BDV actually low or is it contamination picked up during sampling? That’s a different solution all together!
So that brings us to the end of our oil quality assessment trio. In the next few blogs we will look at Furanic Compound Analysis and its relation to Paper Insulation Aging, Understanding PCB and Ensuring Personnel / Environmental Safety and then move onto trending, reporting and Asset Management.