Partial Discharge Testing Frequency: How Often to Test for PD?
-
10 October 2023
-
Thomas Whyte
Understanding the optimal partial discharge (PD) testing frequency is key to maintaining the health of high-voltage (HV) equipment. Regular PD testing helps identify insulation defects early—before they escalate into costly system failures.
What is Partial Discharge and Why Does It Matter?
Partial discharge refers to a localised dielectric breakdown of a small portion of electrical insulation in high-voltage environments. These discharges can occur without completely bridging conductors, but their long-term impact can be significant—leading to equipment degradation, unplanned outages, and safety risks.
The Three Main Types of Partial Discharge
There are three main types of partial discharge, each with its own characteristics and implications:
1. Internal Partial Discharge - The silent killer
Occurs within the insulation itself, without visible or audible signs. It’s the most dangerous and often goes undetected unless condition monitoring is in place.
Tip: Implementing periodic asset condition assessment can help detect internal PD early and extend equipment life.
2. Surface Partial Discharge - A more visible concern
Happens along the surface of insulation, often visible in high humidity conditions. Though easier to detect, surface PD still requires prompt intervention.
Tip: Visual inspections and routine PD testing help manage surface PD risk.
3. Corona Partial Discharge - A Precursor to Surface PD
Typically found in outdoor switchyards and heard as a faint buzzing sound. If ignored, it can trigger surface PD in indoor systems.
Tip: Continuous monitoring is effective for detecting corona and mitigating associated risks.
What is Partial Discharge Testing?
Partial discharge testing is a diagnostic process that measures PD activity to evaluate the insulation condition of HV assets. It allows engineers to detect potential faults before they evolve into failures. PD Testing is an essential part of condition-based maintenance, helping optimise both performance and reliability.
Understanding the P-to-F Curve for Predictive Maintenance
The P-to-F curve (Potential-to-Failure) models how asset degradation progresses. It helps determine the ideal PD testing intervals:
- P (Potential Failure): The point at which a fault is detectable, but the asset is still functioning.
- Condition Monitoring Window: The time between P and F where proactive measures can prevent failure.
- F (Functional Failure): When the equipment breaks down or becomes unsafe.
Given the complexity of HV switchgear and the multiple variables at play, each type of failure or variable may have its own distinct P-to-F curve. It is important to tailor your partial discharge testing schedule to account for these variations and ensure that testing intervals are optimised for early detection.
Factors That Influence PD Testing Frequency
Several variables impact how often you should perform partial discharge testing:
- Type of PD (internal, surface, or corona)
- Type and age of high-voltage asset
- Insulation material (e.g., paper, polymer)
- Discharge amplitude and location
- Environmental conditions (e.g., humidity, temperature)
Asset criticality and network redundancy
Choosing Between Periodic Testing and Permanent Monitoring
Periodic PD Testing
- Recommended annually for most HV assets.
- Ideal for lower-risk equipment or new installations.
- Risk: Faults can develop between testing intervals.
Permanent PD Monitoring
- Offers continuous real-time insight into asset condition.
- Detects evolving faults early.
- Best for critical or ageing infrastructure.
Learn more about EA Technology’s continuous monitoring solutions for PD and condition assessment.
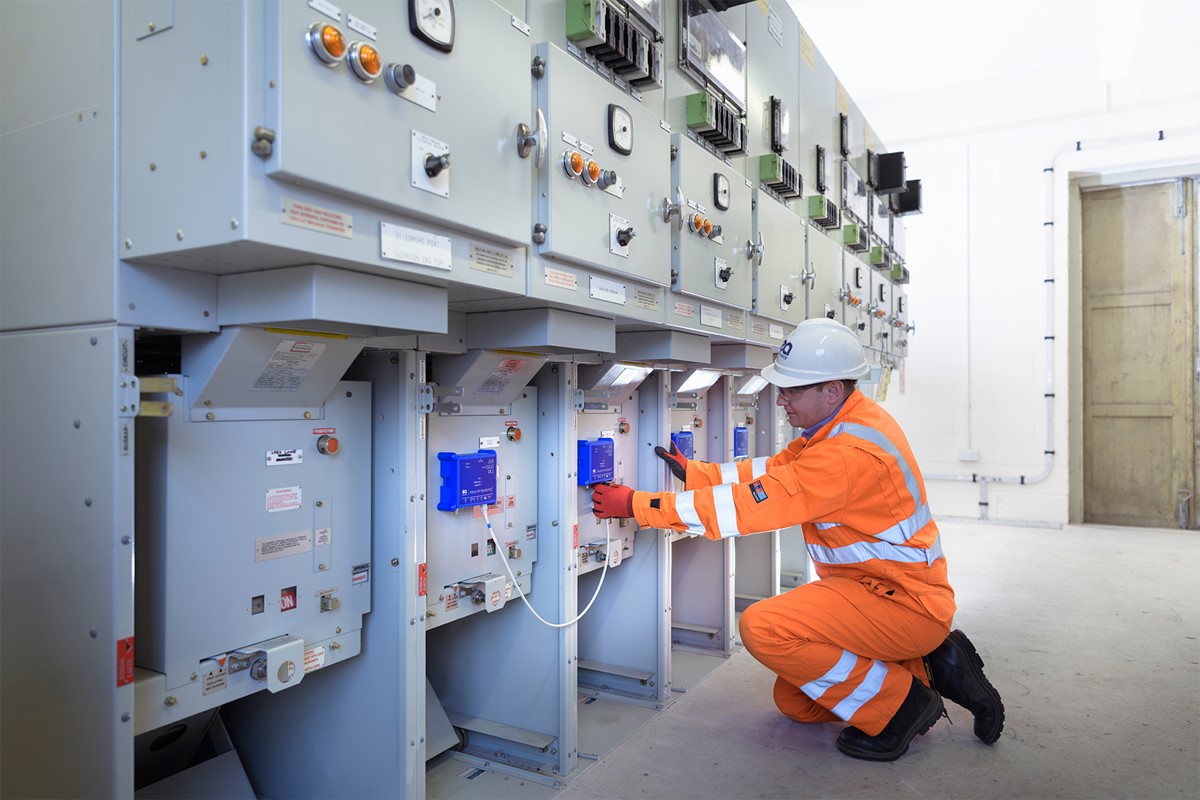