Material Testing for Quality Assurance, Failure Investigation and Condition Assessment
-
09 October 2023
-
Matt Calveley
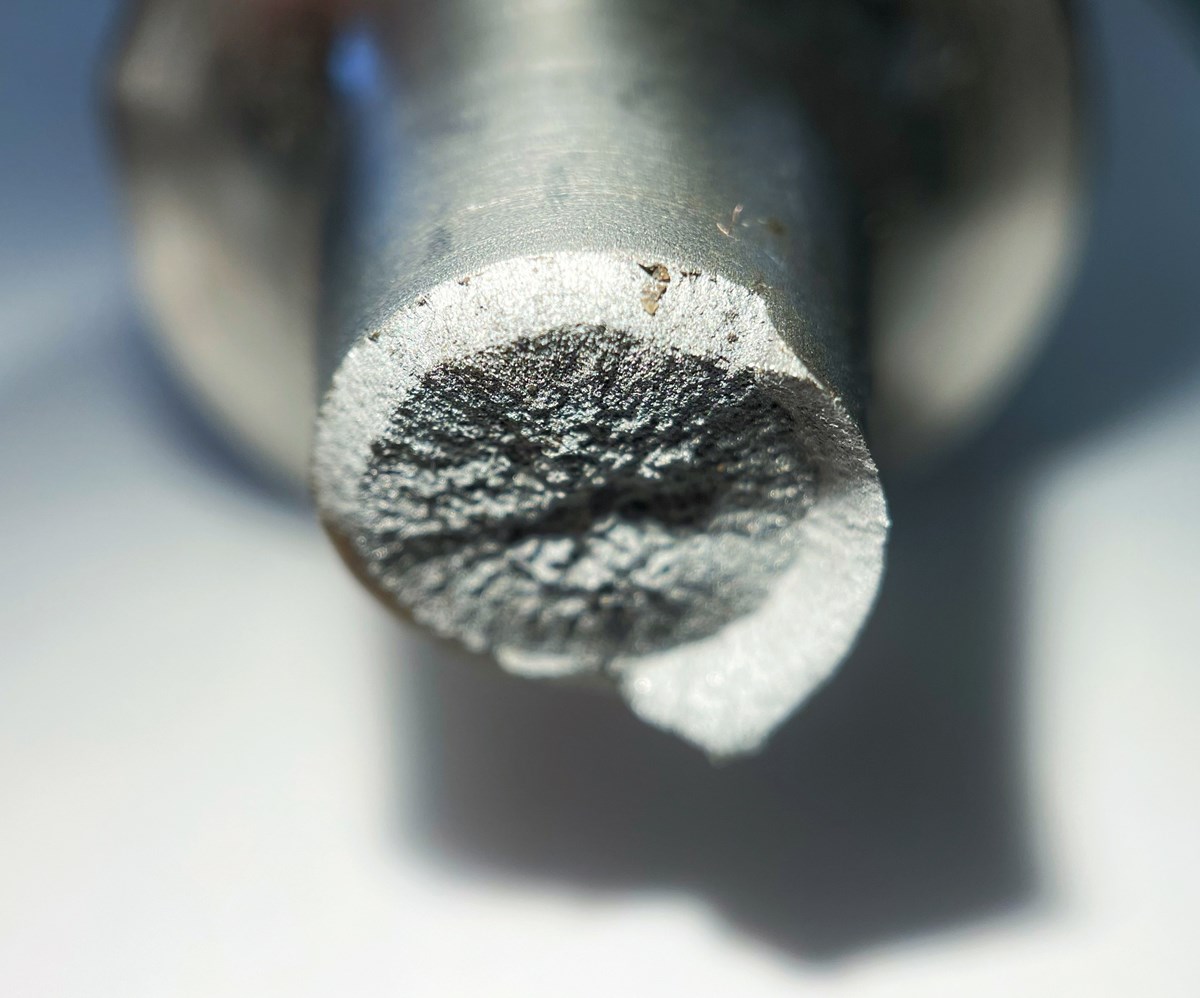
Senior Materials Engineer at EA Technology, Matt Calveley, explores Material Testing of Metals for quality assurance, failure investigation and condition assessment.
We are supported by lots of useful materials to help us in our daily tasks. Whether it’s the phone in your hand, the car you drive or the building you work in, these all require “stuff” made up of different materials.
Every product is designed with materials and in consideration of their specific material properties which helps them in different applications. This might be the strength and toughness of metals for engineering and construction or the versatility of polymers for coatings and packaging.
As consumers and users of products, we all have an intrinsic feel for how different materials should behave. A ceramic mug for example is a very rigid item with a fixed shape and no flexibility. Ideal as a container for hot liquids, but if we drop the mug on a hard floor, it is likely to shatter. If we were to design the mug out of rubber it would be more resilient if dropped, but it might not make for the best thing to hold hot liquids! Ultimately, material choice is often a matter of compromise. This could be cost and ease of manufacture, but it is also a trade off on material properties.
To ensure safety and repeated quality during manufacture the properties of different materials need to be quantified against agreed parameters. For metal components these parameters are things such as strength, toughness, ductility and hardness. The agreed parameters are set by industry experience and through national and international bodies as part of standards or specifications. Material testing is an investigation of these parameters, carried out using a coupon of test material against well-established methods. The idea is that the same tests and methods could be carried out by anyone independently with the same method and equipment. In some circumstances, there are product specific tests that might require a special rig or test apparatus, but for the purpose of this discussion we will just explore the main material tests for metal. Testing is often carried out in house by manufacturers as part of normal quality procedures, but there are situations where independent testing is used such as material verification and failure investigation.
Methods of Material Testing of metal
There are many diverse types of material tests, which can be broadly categorised as Mechanical Testing and Chemical Analysis Testing. Mechanical Tests for engineering properties such as strength and hardness, Chemical Analysis is used to identify the general grade/type of material and can be used to find trace elements which could influence quality.
Methods for the testing of metals include:
-
Tensile Testing
In this test, a sample of material is clamped at either end and pulled apart under load until it deforms or completely separates. Load cells measure the load applied to the sample against displacement to understand the strength and elongation of a sample. This test helps provide information on how strong a material is, where the point of yield may be (a point in which the metal permanently deforms and no longer behaves elastically) and also how ductile the material is.
-
Hardness Testing
Hardness testing is a measure of how resistant to indenting a material is. This can provide an approximation of strength and help understand mechanisms such as wear. There are a few different methods of hardness (including Vickers, Rockwell, Brinell and Knoop), but they all essentially work by creating an indent on the surface of the sample which can then be measured to work out the relative depth of penetration at a particular load.
-
Charpy Impact Testing
Charpy impact testing is a method of determining toughness in a metal. This is a measure of an ability to resist impact and crack propagation. It is applied to metal, in particular applications such as marine and energy and is useful for metals used products such as pipes. A small sample bar is held in place and a large, heavy hammer is swung through it. The energy required to pass through the metal sample is measured as impact energy. In some cases, the metal samples are cooled below subzero temperature to replicate potential service environment conditions and to assess the metal for its ductile to brittle transformation characteristics – this is a situation where a metal becomes much less ductile in very cold environments. Brittle materials are less resistant to crack propagation.
-
Chemical Analysis of Metal
In addition to the mechanical testing described above, chemical analysis of metals helps to confirm the grade of metal - essentially the proportions of elements in a metal alloy, just like a recipe. There are a few ways of doing this which include spark OES, ICP OES, LIBS and XRF. Some techniques are portable and some are more accurate/analytical. The appropriate method depends on the situation and the type of metal to analyse. Small fragments can also be analysed using SEM-EDX.
Material Testing for Quality Assurance
Material testing is applied to a sample coupon material at the point of manufacture and reported as a certificate. The specific tests and standards vary from metal to metal, but in theory all metals components should have a traceability that follows all the way back to the point of manufacture and it is first melted. If this traceability does not exist, then the component can be tested to verify its mechanical and chemical properties using material testing. This can be done under laboratory conditions in an independent laboratory, but also in situ.
Material Testing for Failure Investigation
As part of a failure investigation, material testing can provide information on the quality or specific properties of the components involved. This might help flag quality issues which caused the failure or it may just help to rule out any causative or contributory factors in an investigation. During a failure investigation, the amount of damage or a general lack of material might make testing difficult. In these situations, analytical testing such as SEM-EDX may help.
Material Testing for Condition Assessment
Material Testing can be used for ongoing condition assessment of components. This could be the use of sacrificial samples for the purpose of mechanical testing to determine if there is any loss of properties and to help predict remaining lifetime in the components. At EA Technology we condition assess overhead line conductor samples using mechanical testing to assess loss of ductility with age.
The Future for Material Testing
The techniques for material testing described here are based on well-established methods of quality assurance and investigation. As with any sector, there will be innovations and changes which will enable quicker and more efficient methods of testing. In addition, the development of AI (Artificial Intelligence) will likely enable better use of the data generated from testing and more transparency in the traceability of materials.
If you need independent material testing services EA Technology are here to help you. If you have any questions or would like to learn more about our capabilities, please contact our Forensics team here.