Materials Testing
EA Technology provides a wide range of Materials Testing & Analysis services. We are widely recognised for our independence and quality.
Independent laboratory and forensics services
Benefits
- Validate whether materials and components are fit for purpose
- Check that assets are performing as expected
- Discover why assets have failed
Features
- State-of-the-art laboratories and testing facilities
- Specialist Power Forensics™ failure investigation service
- Expert personnel
Laboratory testing of the mechanical properties of materials is crucial to determine if they meet the demands of the design. These tests are also useful for assessing whether the true performance of materials lives up to the specifications claimed by the manufacturers and to determine the effects of service. EA Technology can offer a range of mechanical tests, including:
- Tensile tests
- Compression tests
- Hardness tests (Vickers Hardness testing)
Tensile characteristics are measured by clamping either end of a sample in the test machine and applying a tensile force to it until the material deforms or fractures. A graph of force vs displacement is generated, from which maximum tensile strength and elasticity are determined. Tensile tests can also be used to determine the mechanical strength of specific components such as cap and pin insulators or overhead line fittings.
Compression tests operate in a similar way, producing a graph of force vs displacement up to and including the point of failure or point of full compression. Characteristics such as optimum and maximum load capacity or spring stiffness can then be determined from the graph.
The Vickers hardness test is used to determine the ability of the material to resist plastic deformation. A sample of the material is placed under a diamond tip indenter with a known applied force. The indenter tip pushes into the material and the hardness is calculated from the load applied and the surface area of the indentation left on the surface.
Optical Microscopy
The optical microscope is a flexible and widely used tool for materials analysis and failure investigation, which provides more detail than an examination by the naked eye, often without any significant sample preparation time. Optical microscopy by our highly-trained personnel can be used to compare a range of materials or components, as well as identify the causes of fractures and material failures.
- Magnification from x5 to x1250
- Can be used non-destructively
- Sample preparation can reveal even more detail
- Can assess dimensions and distributions of particles
- Wide range of applications offered by an expert team
Optical microscopy provides a useful and flexible materials analysis tool, from low magnification observations of up to x40, to high magnification examinations of up to x1250, often with minimal preparation required.
Further preparation, such as cross-sectioning, polishing and chemical etching, can reveal even greater detail of a component’s microstructure. Use of polarized light, phase contrast and Nomarski microscopy techniques is particularly useful when assessing the quality of XLPE cable insulation or other polymer materials.
EA Technology has both the equipment and the expertise to offer a wide range of optical microscopy services, with the experience to deliver maximum value from results through skilled, expert interpretation.
Scanning Electron Microscopy
A scanning electron microscope (SEM), equipped with an x-ray analyser, can produce superior images to those available from an optical microscope, offering far greater magnification and depth of field. Electron microscopy produces an accurate analysis of material surfaces and chemical composition, which is particularly useful in forensic investigations.
- Magnification from x 5 to over x 100,000
- Depth of field up to 1,000 times greater than an optical microscope
- Samples up to 20mm deep and several cm wide can be analysed
- Samples as small as 0.5µm can be analysed
- Detects elements of atomic number 5 (carbon) or greater
The surface of a fracture, seen under an electron microscope, can often reveal a great deal of information about the nature and cause of a fracture. SEM analysis allows examination of the microstructure of a material and its composition. These are useful in accessing the grade of material that has been used in a component or defects in manufacturing. Electron Microscopy can also be used for assessing the quality of and identifying degradation in a wide range of material samples used in the manufacture of electrical network assets and other components.
The addition of an x-ray analyser further enhances this service, allowing us to include analysis of the elements present quickly and easily. This is of particular value in identifying the nature and source of contamination or corrosion.
X-ray photography
X-ray photography (radiography) is used to gain information about inner components of an assembly or piece of equipment before the assembly is dismantled or cut apart. It is particularly useful on assemblies that will split into many pieces when taken apart, making reconstruction of the original structure difficult, such as vacuum circuit breaker bottles or fuses.
The main body of the HV fuse and the two end caps were radiographed in order to determine the condition of the internal components. The fuse element had melted at all the notches and fulgurite had formed. The striker coil had also melted along its length and also adjacent to the striker spring. The melting of the wire should release the spring pushing the striker out of the fuse’s end cap. However, the striker spring was compressed and in the un-operated condition.
The striker end cap was removed in order to examine the striker mechanism. The spring and striker were housed in an aluminium shell, on cutting away the aluminium shell the tension was released from the spring. The striker coil was through the bottom spring coil and had been crimped into a brass joint. The other end of the striker coil passed through a loop in the top of the striker and the melted end was free. The clearance between the striker and the brass insert in the end cap through which the striker should be expelled was too tight and did not allow the striker to pass through.
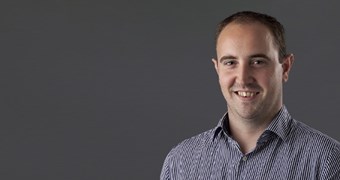

Get in touch
Thank you for your interest in EA Technology. You can request information or a free callback by clicking the link below. One of our experts will be in touch with you shortly.